Paper is made by the pressing together of cellulose fibers originating from wood, straw, bagasse or grasses. The length of fiber is an important factor in the production of paper. Longer fibers form a firmer fibrous web, hence give a firmer paper.

Raw Materials
Wood is the preferred source of raw material around the world, with coniferous trees (spruce, fir, pine etc) having longer, more preferable fiber over deciduous trees (eucalyptus, beech, birch etc.) Wood is debarked and processed in the chipper house of a pulp mill and made into chips or slabs before further processing.
Additionally, waste paper, which is recovered from a variety of sources (see : Major Grades) is also used to make paper. It must be noted that paper cannot be recycled indefinitely. After 4-6 usage cycles, the fibers become short and weak and are not usable for paper making. Some virgin pulp is usually added in processes to maintain the strength and quality of fiber.

Pulping Stage
The first stage of paper making is known as pulping, where the raw material is made into a solution known as "slurry", through either a mechanical or chemical process.
Mechanical pulping involves grinding the raw material against a quick rotating stone under the addition of water. This results in a high yield (95%) but shorter fiber length with higher impurities. Paper which is made using mechanical pulp has high opacity but low strength and light resistance.
Chemical pulping is the process of cooking the raw material to release the pure fiber. The pulp which results from this process can either be sulphate or sulphite in nature, depending on the chemicals used. The yield of this pulp is low (50%) but the resulting fiber length is long and the pulp is clean. Wood pulp made from this process is called "woodfree." Sulphate pulping is used in the case of strongly resinous wood and is chemically intensive. Sulphite pulping is lower strength, but is less chemically intensive with more potential for recycling of chemicals.

Deinking Stage
Board, newsprint, tissue and writing/printing plants which use recovered paper as a raw material pass the pulp into a deinking tower. As the name suggests, this process is used to remove printing, ink and stickies (glues, adhesives etc) from the pulp. This is achieved by a combination of washing and floatation. In a "washing" process, smaller particles of ink are rinsed from the pulp using water. In a "floatation" process, larger particles are removed with air bubbles.

Cleaning and Refining Stage
The first common stage of the cleaning process is to send the pulp to cone shaped, rotating cylinders called centri-cleaners. Here heavy contaminants are moved to the bottom of the cylinder while the lighter contaminants move to the center of the cone. The pulp is then removed from the top of the cylinder.
The pulp is then sent into a refiner or series of refiners to clean the pulp of impurities. The refining stage has an important effect on the type and properties of paper. Pulp is beaten to make the fibers swell. It also separates out large bundles of fibers into individual strands making it ideal for paper making.
Wood pulp which results from the pulping process is brown in colour and has to be bleached in order to obtain the required brightness (in the case of white paper). This is done using chlorine, chlorine compounds and ozone or oxygen. Recycled paper which is coloured has to be color stripped using chemicals.
During this stage of the process, fillers, additives and binders are added to the pulp before it moves to the paper machine. Fillers (calcium carbonate, clay, titanium dioxide etc.) make the paper more opaque, brighter and softer as well as more flexible depending on what the specifications are. Additives such as dyes and optical brightening agents are added as required, depending on the type of paper being made. Binders such as latex and starch are added to improve fiber bonding and coating and ink holdout, to produce better printing paper.

The Paper Machine

![]() |
![]() |
Paper, invented by the Chinese around 2000 years ago, remained a handmade industry till the mid 19th century, when a Frenchman named Louis -Nicholas Roberts, patented the first continuous paper machine. However he eventually lost control on his intellectual property, which resulted in the patent application reaching London in 1801 and shared with stationary shop owners, Henry and Sealy Fourdrinier. For the next few years the brothers worked on the process which would result in the patent for the first Fourdrinier machine in 1804. After 200 years and several technological improvements, this still remains the basis for paper-making. The four main stages of the machine are the wet end, press section, dryer section and the calender section.
The wet end is the stage where pulp is brought to the paper machine from the pulping process. The pulp is made into a 99.5% watery suspension of fibers and is sent into a "head-box". The head-box applies pressure on the pulp which helps to control its flow onto the wire table and also to prevent turbulence at the discharge tip which would lead to frock formation. The liquid pulp that leaves the head-box comes into contact with the "wire-table." The paper fibers move onto the wire as a result of natural flow resistance which causes them to accumulate at the top of the wire as water drains out at the bottom. Sheet formation can be achieved by either filtration or thickening of the fiber solution.
Sheet formation takes place in the wire section of the paper machine. Here more water is drained from the pulp as it moves on a wire table. A "twin-former" wire table allows for drainage of liquid at the top and bottom of the wire. This results in greater efficiency of drainage. A further development known as a "gap-former" incorporates the use of a suction which simultaneously drains water from the top and the bottom by passing the suspension between two wires directly after a head box.
The formed sheets are then sent to the press section to be further drained and compressed. Mechanical pressure is exerted vertically to the sheet surface. This is achieved by running the sheet between a series of rolls which exert set amounts of pressure. The water pressed out of the paper is absorbed by felts and transported off. Recent technological advancements have resulted in the introduction of a "shoe" press, where one roll is replaced by a hydraulically pressed shoe making the process more efficient.
The next stage of the process is the dryer section. The paper which enters is 50-55% dry. The remaining water is removed by contact with steam heated cylinders, using the process of vaporization to remove the water. This section has a series of dryers and the process takes places in stages to prevent a "shock" evaporation resulting in sudden brittleness of the paper.
After it is dried the paper is then sent to machine calendars where it is glazed using steel and soft plastic rolls. This makes the paper surface smooth and glossy. Depending on the type, the paper is ready once it leaves either the calendar or a "coating" machine.
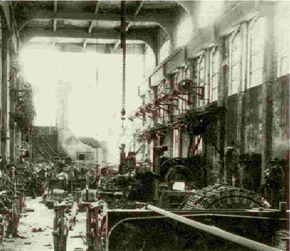

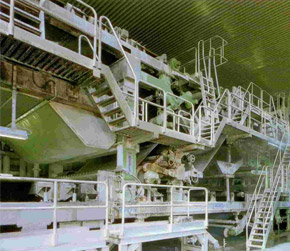


Secure Destruction Services Processing

The paper which exits the machine is then cut into smaller widths using a "slitter rewinder". The slitter consists of circular knives which cut the reels and fits them on different size "tambours" or paper spools. A "sheet-cutter" cuts the rolls into sheets of specific size. In addition to this, modern plants have sheet-cutters which check the quality of surface paper and remove faulty sheets. The paper is then packed in wrappers to avoid damage during transport and provide protection against moisture.
